基于大模型的零部件 在線智能檢測系統(tǒng)
文:文/浙江工商職業(yè)技術(shù)學(xué)院 吳彤2024年第五期
導(dǎo)語: 通過采用人工智能技術(shù)的視覺算法,采用基于Transformer大模型的8層隱含層D-RSN神經(jīng)網(wǎng)絡(luò)算法來解決零 部件形狀缺陷、表面缺陷、包裝缺陷等問題。本項目以滿足所有質(zhì)量要求的無可挑剔產(chǎn)品的圖像樣本為基礎(chǔ), 構(gòu)建了零部件缺陷特征與視覺圖像之間的物理映射機制,將產(chǎn)品可以簡單分類為有缺陷或無缺陷,還可以使用 監(jiān)督學(xué)習(xí)訓(xùn)練模型,以根據(jù)缺陷的嚴(yán)重性、類型或狀態(tài)對缺陷進行分類,這使得能夠創(chuàng)建更復(fù)雜的智能檢測反 應(yīng)機制并收集詳細數(shù)據(jù)。
1 壓縮機概述
當(dāng)零部件在制造企業(yè)生產(chǎn)后期發(fā)現(xiàn)質(zhì)量問題時,就會 導(dǎo)致產(chǎn)品需要再次檢測,此時就會出現(xiàn)時間過長、浪費時 間和精力,這時候就會給企業(yè)帶來巨大的困擾。同時在采 用產(chǎn)品抽檢方式的部分企業(yè)中,由于小概率事件的質(zhì)量追 溯問題也會帶來品牌危機。這時候,如果有一種用于產(chǎn)品 缺陷檢測的“零部件在線智能檢測系統(tǒng)”,它能實時捕獲和 解決產(chǎn)品、包裝或表面缺陷,就能解決用戶的“質(zhì)量缺陷焦 慮問題”。
用于產(chǎn)品缺陷檢測的智能視覺檢測裝置主要解決如下 問題:
(1) 零部件形狀缺陷。損壞的零部件、缺失的零部 件、畸形的零部件、凹陷的零部件、錯誤的組件裝配、尺 寸不符的零部件等。
(2)零部件表面缺陷。顏色檢測、紋理驗證、劃痕和 凹痕檢測、表面畸形檢測、不存在/存在驗證、表面光潔度 檢測、穿孔檢測、撕裂和孔洞檢測。
(3)零部件包裝缺陷。褶皺檢測、標(biāo)簽放置驗證、標(biāo) 簽撕裂或撕裂、包裝損壞、包裝印刷錯誤、蓋子缺失、密 封破損或密封不良、包裝畸形、包裝缺失、瓶蓋缺陷、瓶 蓋傾斜、蓋子安裝檢查、包裝篡改、泄漏檢測。
2 視覺大模型架構(gòu)及其算法
早期的視覺模型采用手工設(shè)計特征和機器學(xué)習(xí)方法解決圖像分類等視覺問題。然而,手工設(shè)計特征局限于像素 層面,損失了過多圖像信息,導(dǎo)致模型的精度較低。與基 于手工特征的方法不同,基于CNN的模型具有強大的特征 提取能力和相對較低的計算復(fù)雜度。2012年,有研究者提 出了基于CNN架構(gòu)的Alex-Net,其在ImageNet圖像識別挑 戰(zhàn)賽中的識別精度首次超越手工特征方法。在此基礎(chǔ)上, VGGNet證明了更深的網(wǎng)絡(luò)結(jié)構(gòu)能夠有效提升模型精度。 ResNet提出在每個模塊中添加殘差連接,以解決深層模型 的優(yōu)化問題,同時引入了瓶頸塊來減少參數(shù)數(shù)量。簡單的 實現(xiàn)和良好的性能使ResNet仍然是當(dāng)今最常用的架構(gòu)。此 外,也有研究者探索了CNN模型的輕量化,MobileNets提 出了深度可分離卷積、反向殘差塊和神經(jīng)架構(gòu)搜索,以實 現(xiàn)更好的精度——復(fù)雜度權(quán)衡。
在輕量化CNN模型應(yīng)用在汽車鋁鑄件等產(chǎn)品的質(zhì)量檢 測時,也存在以下兩個問題:原始模型復(fù)雜度較高,難以 直接部署到資源受限的邊緣設(shè)備上;模型在邊緣設(shè)備上進 行推理的耗時較長難以滿足實際任務(wù)的需求。
為了解決上述問題,引入預(yù)訓(xùn)練技術(shù)來學(xué)習(xí)通用的視 覺表示,以減少訓(xùn)練資源的消耗和訓(xùn)練數(shù)據(jù)的收集成本。 隨著大規(guī)模圖像數(shù)據(jù)集(如ImageNet)的出現(xiàn),探索CV領(lǐng) 域的預(yù)訓(xùn)練模型。預(yù)訓(xùn)練視覺模型在海量圖像數(shù)據(jù)集上進 行預(yù)訓(xùn)練,得到通用視覺特征表示,然后基于較小的下游 標(biāo)注數(shù)據(jù)集對模型進行精細調(diào)整。在微調(diào)階段,模型只需 要消耗較少的訓(xùn)練資源就能取得比從頭開始訓(xùn)練更好的性能,這是因為圖像分割是CV 的一項核心任務(wù),需要識別圖 像像素所屬對象。2023年,MetaAI提出了通用圖像分割模 型,即Transformer大模型,它是基于超過10億個掩模的多 樣化、高質(zhì)量大型分割數(shù)據(jù)集(即SA-1B)進行預(yù)訓(xùn)練,利 用Transformer或Prompt Engineering來處理下游分割任 務(wù),這使其能夠泛化到從未見過的新對象和圖像類型,且 不需要對下游任務(wù)進行微調(diào)。
如圖1所示,Transformer大模型以滿足所有質(zhì)量要求 的無可挑剔零部件產(chǎn)品的圖像樣本為基礎(chǔ),使用大型圖像 數(shù)據(jù)池訓(xùn)練集進行訓(xùn)練,深度學(xué)習(xí)模型可以解釋給定圖像 的內(nèi)容,該機制在制造過程中用于缺陷和異常檢測。本項 目所構(gòu)建的拓撲結(jié)構(gòu),可以學(xué)習(xí)識別不同類型的缺陷。設(shè) 備捕獲的圖像將基于其進行評估,如果不匹配,則會立即 標(biāo)記缺陷,實現(xiàn)圖像缺陷特征全息感知。
大模型架構(gòu)由多個編碼器和解碼器疊加構(gòu)成,每個編 碼器由2個基本模塊組成,即MSA模塊和前饋全連接(Feed Forward Network,F(xiàn)FN)模塊。MSA模塊利用自注意力 機制學(xué)習(xí)輸入序列內(nèi)部的相關(guān)關(guān)系,F(xiàn)FN模塊包含激活函數(shù) 和2個線性層,MSA模塊和FFN模塊均使用殘差連接和層歸 一化(Layer Normialization,LN)結(jié)構(gòu)。
給定輸入序列x 0 ,第k個編碼器的輸出如下:
式中:xpos表示位置嵌入, x k表示第k個編碼器的輸 出。解碼器與編碼器的結(jié)構(gòu)稍有不同,由二個多頭自注意 力模塊和一個前饋全連接模塊組成,其中一個MSA模塊增加了單向注意力掩碼,使得輸入嵌入向量只能關(guān)注過去的 嵌入向量和它本身,確保預(yù)測結(jié)果只依賴于已生成的輸出 詞元,然后,掩碼多頭注意力模塊的輸出和編碼器的輸出 通過第二個MSA模塊進行處理。
有了Transformer大模型后就可以創(chuàng)建生成異常檢測 算法,如采用包含8層隱含層的D-RSN(Deep Residual Shrinkage Networks,即深度殘差收縮網(wǎng)絡(luò))神經(jīng)網(wǎng)絡(luò)算法。
這里先初始化D-RSN的深度、節(jié)點數(shù)、網(wǎng)絡(luò)學(xué)習(xí)速 率、網(wǎng)絡(luò)序列長度等參數(shù),通過對時間正序數(shù)據(jù)池訓(xùn)練集 分區(qū)進行訓(xùn)練,利用內(nèi)部有監(jiān)督機制進行特征微調(diào),持續(xù) 進行迭代循環(huán),使先驗時序數(shù)據(jù)可以學(xué)習(xí)到未來時序數(shù)據(jù) 的特征,實現(xiàn)較長周期內(nèi)的圖像缺陷特征全息自主感知。 為了加快D-RSN的收斂進程,避免梯度發(fā)散現(xiàn)象,利用 粒子群優(yōu)化算法對D-RSN的初始值進行反復(fù)優(yōu)化,定義 D-RSN預(yù)測的均方誤差MSE作為適應(yīng)度函數(shù),則D-RSN預(yù) 測局部最優(yōu)解的均方誤差(MSEi)和D-RSN預(yù)測全局最優(yōu) 解的均方誤差(MSEg)分別為:
式(1)、(2)中:P為數(shù)據(jù)池訓(xùn)練集分區(qū)的數(shù)據(jù)數(shù); N為D-RSN的節(jié)點數(shù);N為PSO的粒子數(shù)disy和yisj分別為預(yù) 測數(shù)據(jù)集和真實數(shù)據(jù)集。
機器視覺圖像缺陷自主檢測及輸出算法將D-RSN生成 的時間正序下的機器視覺圖像缺陷特征隱性知識數(shù)據(jù)集作 為學(xué)習(xí)數(shù)據(jù)集,實現(xiàn)機器視覺圖像缺陷自主檢測,引入神 經(jīng)網(wǎng)絡(luò)對數(shù)據(jù)池后置測試集進行圖像缺陷自主檢測,利用 隱性知識數(shù)據(jù)集對圖像缺陷檢測結(jié)果進行邏輯修正,借助 圖像缺陷定位及分類函數(shù)輸出檢測結(jié)果。
此時,定義數(shù)據(jù)池測試集分區(qū)圖像缺陷輸出函數(shù)為Y (j,k),定義修正過的數(shù)據(jù)池測試集分區(qū)圖像缺陷輸出函 數(shù)為X(j,k),神經(jīng)網(wǎng)絡(luò)的激活函數(shù)采用sigmoid函數(shù)并定 義為f,則有:
式(3)、(4)中: ξ為神經(jīng)網(wǎng)絡(luò)的深度;ki,j 為網(wǎng)絡(luò) 核;yi為修正系數(shù);*表示平面網(wǎng)絡(luò)操作;bj為偏置誤差; pj為輸入的圖像缺陷數(shù)據(jù)集;β為修正權(quán)重;down(·)為 池化采樣函數(shù)。
上述公式構(gòu)建了零部件缺陷特征與視覺圖像之間的物 理映射機制,將產(chǎn)品可以簡單分類為有缺陷或無缺陷,還 可以使用監(jiān)督學(xué)習(xí)訓(xùn)練模型,以根據(jù)缺陷的嚴(yán)重性、類型 或狀態(tài)對缺陷進行分類。這使得能夠創(chuàng)建更復(fù)雜的智能觸 發(fā)反應(yīng)機制并收集詳細數(shù)據(jù)。
3 零部件在線智能檢測系統(tǒng)的應(yīng)用
通過大模型部署到零部件在線檢測系統(tǒng)中,取得了預(yù) 期的穩(wěn)定性、可靠性。
以被測25mm的零部件產(chǎn)品尺寸為例(圖2、3),為 保證0.01mm以下檢測精度,視覺相機采用1200萬像素。 該部件為金屬材質(zhì),為避免零部件本身的環(huán)境光與金屬反 光對測量的干擾,將采用“黑白相機+背光光源”的模式進 行補光。測試DEMO如圖4所示。
如圖5、6、7所示,該工作流程如下:
① 當(dāng)CNC加工完成后通過桁架式機器人將成品件運輸 至檢測位置;
?、?三爪氣動氣缸將部件球頭部分夾持,中心孔氣缸頂 出定位;
?、?桁架式機械手離開檢測位置,視覺傳感器進行識別 檢測;
?、?檢測完畢后縮回中心孔氣缸和松開三爪氣缸,零部 件落入工作臺的部件中轉(zhuǎn)盒中;
?、輽z測結(jié)果展示。
檢測合格:屏幕中顯示“OK”,不報警;檢測不合 格:屏幕中顯示“NG”,系統(tǒng)觸發(fā)聲光報警;不良品處 理:系統(tǒng)觸發(fā)報警后,聯(lián)動上下料機械手停止運行,當(dāng)工 人將不良品移除后系統(tǒng)恢復(fù)運行。
4 結(jié)束語
創(chuàng)新點一:采用大模型基礎(chǔ)上的D-RSN算法
借助大模型架構(gòu),可以更有效地評估其產(chǎn)品質(zhì)量,而 無需考慮因為人工檢測帶來的一致性缺乏問題。機器學(xué)習(xí)采用大模型基礎(chǔ)上的D-RSN算法,具體如圖8所示。該方法 避免了對圖像的復(fù)雜前期預(yù)處理,可以直接將原始圖像輸 入,降低網(wǎng)絡(luò)模型的復(fù)雜度,減少權(quán)值的數(shù)量。采用局部 連接和共享權(quán)值的方式,使網(wǎng)絡(luò)易于優(yōu)化,也降低了過擬 合的風(fēng)險。
創(chuàng)新點二:可以個性化機器學(xué)習(xí)模型
雖然市場上有很多現(xiàn)成的視覺檢測系統(tǒng),但本項目使 用基于大模型的個性化機器學(xué)習(xí)模型。原因很簡單,由于 缺陷檢測具有不同的特征,個性化學(xué)習(xí)模型可以使用自己 的訓(xùn)練數(shù)據(jù)集來訓(xùn)練系統(tǒng),提取缺陷固定區(qū)域以提高準(zhǔn)確 性,而現(xiàn)成的系統(tǒng)通常不提供這種可能性。圖9所示為用于 插接端子的個性化機器學(xué)習(xí)模型。
基于大模型的零部件在線智能檢測系統(tǒng)能夠根據(jù)邊緣節(jié) 點的計算能力以及檢測頻率的要求,在單一節(jié)點上同時運行 多個不同的算法。此外,該系統(tǒng)還允許通過云平臺進行算法 的升級和替換等操作,以靈活地應(yīng)對不同產(chǎn)線質(zhì)量檢測場景 的需求。這種系統(tǒng)的特點在于其簡潔的結(jié)構(gòu)、靈活的部署方 式以及可視化的運維管理,可以有效地支持傳統(tǒng)零部件產(chǎn)業(yè) 向數(shù)字化智能化轉(zhuǎn)型。
中傳動網(wǎng)版權(quán)與免責(zé)聲明:
凡本網(wǎng)注明[來源:中國傳動網(wǎng)]的所有文字、圖片、音視和視頻文件,版權(quán)均為中國傳動網(wǎng)(www.wangxinlc.cn)獨家所有。如需轉(zhuǎn)載請與0755-82949061聯(lián)系。任何媒體、網(wǎng)站或個人轉(zhuǎn)載使用時須注明來源“中國傳動網(wǎng)”,違反者本網(wǎng)將追究其法律責(zé)任。
本網(wǎng)轉(zhuǎn)載并注明其他來源的稿件,均來自互聯(lián)網(wǎng)或業(yè)內(nèi)投稿人士,版權(quán)屬于原版權(quán)人。轉(zhuǎn)載請保留稿件來源及作者,禁止擅自篡改,違者自負版權(quán)法律責(zé)任。
如涉及作品內(nèi)容、版權(quán)等問題,請在作品發(fā)表之日起一周內(nèi)與本網(wǎng)聯(lián)系,否則視為放棄相關(guān)權(quán)利。
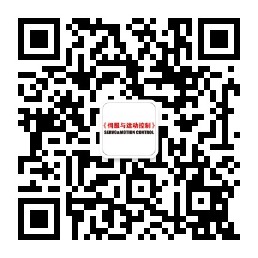
關(guān)注伺服與運動控制公眾號獲取更多資訊
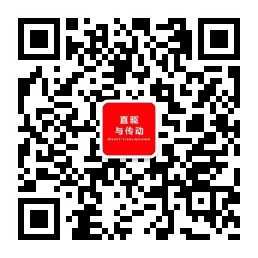
關(guān)注直驅(qū)與傳動公眾號獲取更多資訊
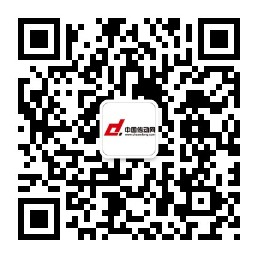
關(guān)注中國傳動網(wǎng)公眾號獲取更多資訊
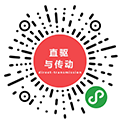
掃碼關(guān)注小程序
時刻關(guān)注行業(yè)動態(tài)

- 1資訊在線

填寫郵件地址,訂閱更多資訊:
撥打電話咨詢:13751143319 余女士
郵箱:chuandong@chuandong.cn
- 運動控制
- 伺服系統(tǒng)
- 機器視覺
- 機械傳動
- 編碼器
- 直驅(qū)系統(tǒng)
- 工業(yè)電源
- 電力電子
- 工業(yè)互聯(lián)
- 高壓變頻器
- 中低壓變頻器
- 傳感器
- 人機界面
- PLC
- 電氣聯(lián)接
- 工業(yè)機器人
- 低壓電器
- 機柜